I began carving with the Tagua Nut and I know why my tutor at the time introduced us to carving through it, the Tagua Nut I feel is a great material for beginners to learn from.
About the Tagua Nut - The Tagua Nut comes from the Ivory nut palm found in the tropical rainforest's of South America, it has a brown outer layer and also has a little hole that can get in the way of carving, so when designing you should think about how to incorporate it. They vary in size but for the most part are the size of large plums, over time the color of the nut darkens and I've also noticed some shrinkage.
You can probably find the nut at your local woodturner shop for a few bucks each, if not they could probably ship some in, you can also order them online.

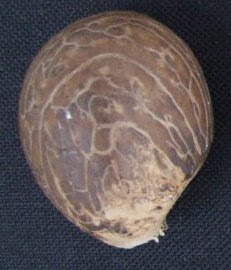
Preparation - There really isn't much, sand off the outer brown layer to reveal the ivory colored material and you're ready to go.
Tools - A lot of people use power tools such as Dremels to shape their carvings along with fine sand paper, needle files, vices and grips. I'm a hand tools man myself and use homemade tools for my shaping.

How to make the Tool - The hand tools I use I made myself, they comprise of a hard tool grade steel (Cobalt Super Blank Stock, most probably), epoxy glue and wood for the handle. I've only made these tools once, I made a set and I'm still using the same set, so the process of making them is a little hazy. The one aspect I'm a little hazy on is if I heated the steel to make it harder. I've searched on the net for the tools I made but haven't been able to find an exact match, I maybe giving away someones secret, sure hope not. The closest I could find were Gravers, but they have a straight edge and I haven't used them before, they look like they could give the same result.
Making the tool should be straight forward, get a piece of wood, drill a hole for the steel to fit into, fill it with epoxy glue and force the the steel into it and let it dry. After that you can shape the handle to fit your hand and create the point on the steel that you'll be using to carve.





What you want is two curved edges that come to a point like in the photos provided, use a grind wheel to get the desired shape and then a fine grind stone to get it sharp and smooth.
Carving the Nut - The great thing about the Tagua is it has no real grain to it, so no matter where you go with the nut it wont resist, unlike materials such as wood and bone where you have to take into account the direction of the grain for your designs.
The other thing to take into account is the little hole that each nut has, some cases you can sand it out, but because there's not much of the nut to work with anyhow, incorporating the hole can be a challenge.
With power tools the job can be quick, shape it out, file it and sand it to a final product, you may have to use vices and grips to stabilize the nut. The thing I don't like about using power tools is a lot of the time it comes out looking machine made, but I guess it all depends on how good the user is with the tool. This is why I like using hand tools, you get much more fine controls over the shaping, you get to take your time with the material for best possible results.
So using the hand tool that I described how to make could be a little hard to explain unless shown, but I'll try my best.
There are two main types of positions with this tool, the first is using the point like a chisel, pushing through the material to make a groove, though with the Tagua you may find it can chip is as you go. The second is by using the curved edge to push along the surface of the material, cutting slightly into the material while allowing the tool to follow its own curve, pretty much shaving flakes from the nut, this way you can be less concerned about chipping.
After you're happy with a form you like, all that's left to do is sand paper it to your desired smoothness and you're done, maybe a little polish.
Here's a carving of a Griffin that's about half way done followed by a selection of nuts.


So I hope you liked my little guide on how to carve with Tagua, I'm sure you could take the entire thing as a metaphor for something dirty, LOL I sure hope not. I feel that carving with Tagua Nuts can be a very easy, hastle free experience for beginners and experts alike, it's one great resource.
If you have any question or suggestions (I'm sure I've left something out) please feel free to leave a comment.
Wow, excellent carvings Rand, very impressive, good tutorial as well.
ReplyDeleteCheers Bob, took me awhile to get it together, had another motive though, I'm hoping a carver comes along a corrects me on the tool making, it's as easy as I described, I just don't know about the heating part, can't remember at all.
ReplyDeleteNice site, and clear instructions. I was gifted with a few Tagua nuts, and thought about carving buttons and pendants. Any suggestions on how best to hold these steady?
ReplyDeleteHi jrquints, I've mainly only ever carved holding the material in my hands which suits my style, I'm usually all over the place and find clamping the materials down a hastle, unless I'm using power tools or saws which is actually very rarely.
ReplyDeleteI've done some jewellery making in the past as well and I'd say that's of a similar scale to what you have in mind, in that case I used small g-clamps and small blocks of wood with wedges cut out of them to provide room to work. You just clamp these pieces of wood to a sturdy workbench and pretty much learn to use it, it can be tricky to get used to so be careful, punctured myself a few times like this, it's why I avoid working that way lol.
The carvings I do are small, but they're still at a scale where it's perfect to work them by hand, they're for the most part free form and not symmetrical, the reason for that is I don't want to clamp them, work them at a desk.
I'm right handed and I carve the tagua with it in my left hand and the tool in my right, I usually use my left thumb to push the tip of the tool across the nut, this is with the curved edge of the tool to flake away pieces of the nut.
If I want to create a "ditch", "reservoir", "line", I can't find the right word, I kind of use both hands to leverage each other to push the point of the tool to dig a line, then I use the flake way to smooth the edge out.
Most of the time both my hands are always in contact with each other to provide steadiness and control.
Sorry, it's way past my bedtime and after just writing all that I've just clicked to something that could possibly summarize it nicely, I'd say my process is a lot like "Whittling", different tool, possibly a very similar way of carving, especially in the detail work and especially with the tools I describe which are tools for very fine detail and control.
Probably could have put it all a lot better after a good nights sleep lol.
Cheers Rand.
Hi... thank you so much for sharing your wisdom! i was wondering, i have heard that these nuts are originally soft then as they are dried they harden. do you typically carve when they are soft, hard, or in between? and do you know if these palms can be grown in the united states? Thank you so much!
ReplyDeleteHey, this is a great article on tagua carving! I've had a little tagua penguin since I was a kid and I've always kinda thought it'd be cool to learn to carve the nuts. Do you think I can buy tools like yours anywhere? I don't really know of any woodworking shops around me, so i don't know what I'm looking for or where.
ReplyDeleteWoooooooooooooooooooooooooooooow /Hey thanks man!! you are so good. I think this the perfect work.
ReplyDeletePower Tools
Thanks for the info! Great Tutorial!
ReplyDeleteTo heat treat (harden), first heat the metal up to red-hot with a torch, then dip it completely in oil or water. Don't heat it up past a dull red or it will burn I use peanut oil. Once it is cooled, it will be very hard and brittle, so put it in a toaster oven at 400 degrees for an hour, then leave it to cool slowly, and it will temper the steel. Probably best to do this after the edge is shaped and initially sharpened, but before attaching to a handle. I use this method for wood carving knives and chisels.
ReplyDelete3/1/2014:
ReplyDeleteThis week I purchased some tagua nuts to use as practice for some hard-stone carving I'd like to do. I have a couple (purchased) carved tagua netsukes that I have always liked and find the surface quite pleasing....
But then, looking at that big spotty bean, I realized that I really know very little about them. So Here I found your tutorial and it is very informative.
Thanks for the info on tools, I have quite a few and can always use a couple more! I am guessing that you did not initially heat your tools, as the color of the steel would probably show the tempering as a blue to straw shift from the handle end to the tip. I doubt that for tagua that tempering would be necessary- but for carving hardwoods, especially those that contain a lot of silicates, it might be a good idea.
Your previous poster gives good advice. Another way that some folks temper is to bury their tool in a can of dry sand and let it cool slowly. Make sure its a big enough can to completely surround the tool by a couple three inches from the can wall. Either way works.
Thanks for the tutorial!
What do you polish it with? A type of nut oil on a cotton ball, a special kind of polisher, or something else?
ReplyDeleteThanks so much for this post! A friend just sent me 10 of the little buggers that I intend to use as Netsuke. I've been trying not to hack off my fingers using my micro Flexcuts, but yours is by far, a much more tangible (and more my style of as few power tools as possible). One question though, where did you get the steel blanks for your gravers? I have some old chisels I won't mind recycling, but if there's a source for smaller blanks I'd greatly appreciate the info as much as I do this post!
ReplyDelete